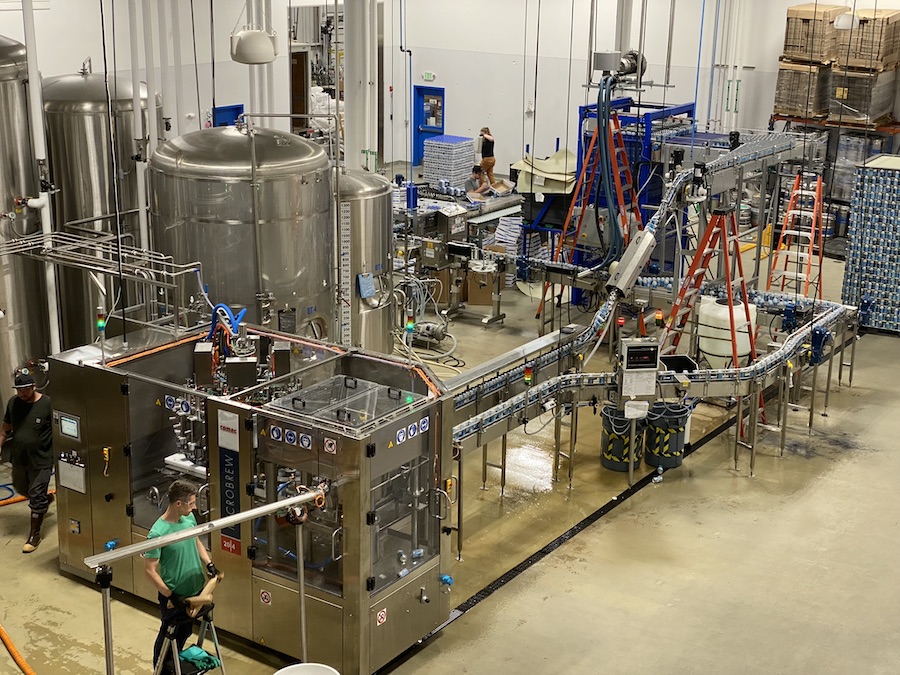
Our new canning line (featuring Chuck Norris)
We’ve been planning for a new canning line in the brewery for a long time, so when a crane rolled in hauling eight tons of equipment this summer, we were all pretty stoked.
The new canning line is fully automated – and it is fast. Our previous canning line filled about 70 cans a minute. At full throttle, the new one can fill up to 200 per minute! Plus, the new filler has reduced our waste by 8%.
The new system also uses a laser to check the levels of each can, and if a can doesn’t measure up (literally) then it gets kicked to the curb (almost literally). The HUEFT Basic fill level and closure detector with failure ejector – a.k.a. Chuck Norris – replaces the previous process of operators eyeballing fill levels. It’s more accurate, less wasteful, and a better experience for our packaging crew. System sensors communicate with each other all along the line, which makes the entire operation easier and the job more enjoyable.
Perhaps the biggest benefits of the new canning line are the ways it reduces the beer’s exposure to oxygen; the DO (Dissolved Oxygen) is substantially less because the filler fills volumetrically. It also cools the cans in a sealed environment instead of an atmospheric environment, which helps evacuate any air in the can, making the liquid inside the can more stable. That means the beer stays fresher, longer.
We’ll keep making investments in our brew technology as long as it keeps making the beer better and our brewery a better place to work.